목표 : 3월 28일에 CPIM Part 1 취득하기
1. introduction to material management
manufactuing creates walth by adding value to goods. to improve productivity and wealth, a company must first design efficient and effective systems for manufacturing.t must then manage these system to make the best use of labor, capital, and material.one of the most effective ways of doing this is through the planning and control of the flow of materials into, through and out of manufacturing. there are three elements to a material flow system : supply, manufacturing planning and control, and physical distribution. they are connected and what happens in one system affects the others.
traditionally there are conflicts in the objectives of a company and in the objectives of marketing, finance and production. the role of materials management is to balance these conflicting objectives by coordinating the flow of materials so customer service is maintained and the resources of the company are properly used.
key-term
- assemble- to - order
- available facilities
- bill of material
- channel master
- configure-to-order
- engineer-to-order
- enterprise resource planning
- implementation and control
- inventory management
- make-to - order
- make- to- stock
- materials management
- metric
- orchestrator
- order qualifiers
- order winners
- performance measure
- performance standard
- postponement
- process specfications
- product description
- production planning
- quantities required
- reverse logistics
- routing
- standard time
- supply chain management
- work-in- process (WIP)
2. production planning system
Production planning is the first step in a manufacturing planning and control systme. the planning horizon usually extends for a year. the minimum horizon depends on the lead tiems to purchase materials and make the product. the level of detail is not high. usually , the plan is made for families of products based on the similarity of manufacturing processes or on some common unit. the production plan is part of the sales and operations planning process, which is an executive-level planning process involving trade-offs across department or functions in the company.
three basic strategies can be used to develop a production plan;chase, leveling producton, or hybrid. each has its operational and cost advantages and disadvantages.it is the responsibility of manufacturing management to select the best combination of these basic plans so total costs are minimized and customer service levels are maintained.
a make to stock production plan determines how much to produce in each period to meet the following objectives;
- achieve the forecast
- maintain the required inventory levels
although demand must be satisfied, the plan must balance the cost of maintaining inventory with the cost of changing production level.
a make to order production plan determines how much to produce in each period to meet the following objectives.
- achieve the forecast
- maintain the planned backlog.
the cost of backlog that is too large equal the cost of turning away business. if customers have to wait too long for delivery, they might take their business elsewhere. as with a make to stock production plan, deman must be satisfied, and the plan must balance the cost of changing production levels with the cost of backlog that is larger than desired.
key terms
advanced planning and scheduling (APS) system
Aggregate production plan
backlog
backorder
balanced scorecard
business plan or strategic business plan
capacity
chase stratey
enterprise resource planning
green production
hoshin planning
hybrid strategy
key performance indicators
level production plan
manufacturing resource plan
master production schedule(MPR)
Material requirement plan(mrp)
priority
production activity control(PAC)
production leveling
production plan
resource bill
resource planning
remanufacturing
reverse logistics
reverse supply chain
risk management
sales and operations planning(SOP)
Social responsibilty
strategic plan
subscontracting
sustainability
united nations global compact
3. master scheduling
the master production schedule is a plan for the production of individual end items. it must match demand for the product in total. but it is not a forecast of demand. the MPS must be realistic. it must be achievable and reflect a balance between required and available capacity.
the MPS is the meeting ground for sales and production. it provides a plan from whcih realistic delivery promises can be made to customers. if adjustments have to be made in deliveries or the booking of orders, they are done through the MPS.
Master production scheduling's major functions are to form a link betw the production plan and the facility, as an input to plan capacity, as teh major input to MRP, to help make order promised, kepp priorities valid, and be a major link btw production and sales.
the MPS must be realistic and based on what production can and will do. if it is not, the results will be as follows;
overload or underload of plant resources
unreliable schedules resulting in poor delivery performance
high level of work-in process inventory
poor customer service
loss of credibility in the planning system
key term
available to promise (ATP)
Demand time fence
Final assembly schedule (FAS)
Frozen zone
liquid zone
master production schedule(MPS)
Planning time fence
psotponement
projected available balance (PAB)- among the customer order, the forecas.
rough-cut capacity planning
scheduled receipts
slushy zone
4. material requitement planning
the job of the MRP is to produce the right components as the right time so that the MPS can be maintained. the MRP depends on accuate bills of material and on accurate inventory records. bill of material can be created in many ways, but one department(or individual) must be responsible for them. inventory records are indispensable to the MRP, and the MRP is only as good as the inventory records.
the MRP exploding and offsetting processes outlined in this chapter are largely done by the computer. the logi used is repetitive and while error prone when done by individuals can be accomplished well by computer. good MRP practice is achieved by planners being able to work with the system.
the MRP process uses the bill of materials that lists components used to make a product, the lead time to make or obtain those components, and the existing inventory of those components to calcualate a series of planned order releases to obtain or make components to meet future product needs.
key term
action bucket
allocate
bill of material
bottom-up replanning
bucketless system
component items
dependent demand
exception message
exploding
firm planned order
independent demand
indented bill
inventory record
lead time
low-level code
master production schedule
material requitements planning(MRP)
Multilevel bills
multiple bill
net requirements
offsetting
open orders
paren
pegging report
planned orders
planned order receipt
planned order release
planning bills
planning factors
planning horizon
product tree
reducing system nervousness
releasing an order
scheduled receipts
single-level bill
summarized parts list
time buckets
transaction message
where-used report
5. capacity management
capacity management occurs at all level of the planning process. it is directly related to the priority plan and the level of detail and time spans will be similar to the related piority plan.
capacity planning is concerned with translating the priority plan into the hours of capacity required in manufacturing to make the items in the priority plan and with methods of making that capacity available. capacity available depends upon the number of workers and machines, their utilization and efficiency,
capacity requirements planning occurs at the material requirements planning level. it takes open shop order and planned order from the MRP and convert them to a load on each work center. it considers lead times and actual order quantities. it is the most detailed of the capacity planning techniques.
material requirements planning and capacity requirements planning should form part of a closed-loop systme that not only includes planning and control functions but also provides feedback so planning can always be current.
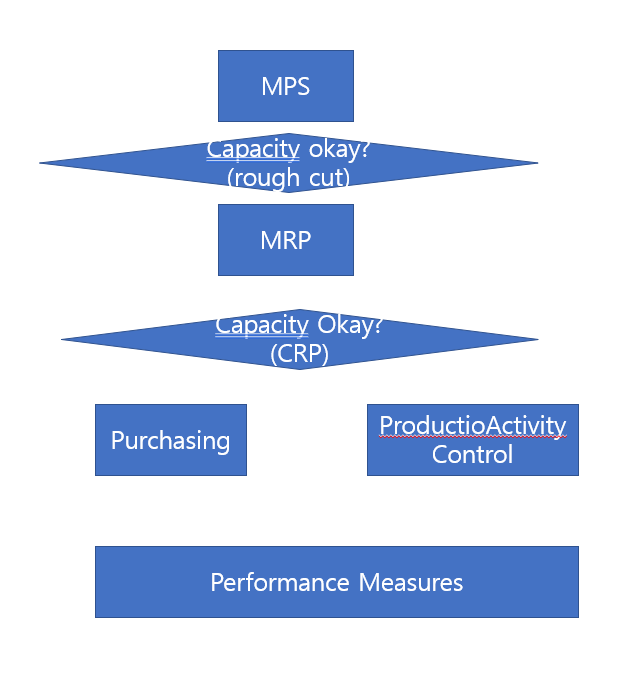
key terms
available time
back scheduling
backward scheduling
calculated capacity
capacity
capacity available
capacity control
capacity cushion
capapcity management
capacity planning
capapcity required
capacity requirements planning (CRP)
demonstrated(measured) capacity
efficiency
forward scheduling
lead time
load
load report
move time
open order
planned order
productivity
queue time
rated capacity
resource planning
rough-cut capacity planning(RCCP)
routing
safety capacity
scheduling
shop calendar
standard hours
standard time
theoreical capacity
utilization
wait time
work center
6. production activity control
production activity control is concerned with converting the material requirements plan into action, reporting the results achieved, and when required, revising the plans and actions to meet the required results. order release, dispatching, and progress reporting are the three primary functions. to accomplish the plans, PAC must extablish detailed scheduls for each order, set priorities for work to be done at each work centerm and keep them current. production activity control is also responsivle for managing the queue and lead times. nonmanufacturing industirs must also control capacity and inventory in order to monitor progress, manage resources and derive appropriate schedules.
the theory of constraints modifies the approach to PAC since it views a production facility , the suppliers and the market as a series of interdepent function. TOC attemps to optimize the constraints(bottlenecks) in a system as they affect the overall throughout. as a result, traditional lot sizing ruels should be modified to increase the throughput of the entire process and not just the individual work center. drum-buffer- rope describes how the TOD works by setting an overall pace of material flow, ensuring bottlenecks never run out of material and linking the output of one work center to another. measurement system are used by PAC to monitor and control progress, meet delivery dates, utilize labor and equipment efficiently, and keep inventory level down
key terms
backward scheduling
bill of material
bottlenecks
continuous manufacturing
critical ratio(CR)
cumulative variance
cycle time
dispatching
drum-buffer-rope
earliest job due date
earliest operation due date
finite lading
first come, first served.
flow manufacturing
forward scheduling
gateway operation
infinite loading
input/output control
input/output report
intermittent manufacturing
item master
load profile
manufactuing lead tiem
move time
operation overlapping
operation splitting
process batch
product strutre
product tracking
project manufactuing
queue tiem
repetitive manufactuing
routing
run time
setup time
shop order master
shortest process time
slack per operation
slack time
throughput
throughput time
transfer batch
wait time
work center master
7. purchasing
purchasing has always been an important function in any company, especially manufacturer who use a lot of ras materials or materials that are difficult to obtain. purchasing needs to continue to get the right products at the right time and at the best price but, the function is changing. the steps in the purchasing cycle are still necessary but many manual activities such as writing PO, getting inforamtion on product, and communication with suppliers have been sped up through use of the internet and computerization. the reduction in routine clerical activity allows time to take a more strategic view of the organization and have an increasing impact on profits. viewing the supply chain as an integrated function, outsourcing and lean production are three management influences that have encouraged purchasing to improce their relations with suppliers and to take a more active role in the scheduling and flow of products. purchasing also has the opportunity to take a lead role in reducing the enviormental impact of a company by working with suppliers and the use of environmentally friendly materials.
key terms
break-even point
bullwhip effect
by-product
commodities
contracat buying
customer relationship management(CRM)
Electronic data interchange(EDI)
Engineering drawings
enterprise resource planning
enviornmentally responsible purchasing
extranet
fair price
fixed costs
functional specifications
internet
intranet
landed cost
maintenance, repair and oeprating supplies (MRP)
Mutiple sourcing
offshoring
outsourcing
planner/buyer
purchasing cycle
purchasing requisition
reduce,reuse, and recycle
request for quote(RFQ)
reverse logistics
single sourcing
sole sourcing
standard specification
supplier flexibility and reliability
supplier ranking
supplier relationship managemnet
total cost of ownership
value analysis
vairable costs
vender-managed inventory(VMI0
8.forecasting and demand management
forecasting is an inexact science that is nontheless an invaluavle tool if the following are kept in mind;
forecasts should be tracked
there should be a measure of reasonableness of error
when actual demand exceeds the reasonableness of error, an investigation should be made to discover the cause of the error
if there is no apparent cause of error, the method of forecasting should be reviewed to see if there is a better way to forecast.
there are several methods used to forecast, including qualitative, quantative, intrinsic, and extrinsic methods.
key terms
average demand
bias
collaborative planning, forecasting, and replenishment(CPFR)
demand lead time
demand management
deseasonalized demand
dynamic
economic indicators
exponential smoothing
external forecasting techniques
forecast error
internal forecasting techniques
leading indicator
mean absoulte deviation
moving average
normal distribution
order processing
production lead time
qualitative/quntitative techniques
random variation
seasonal index
seasonality
smoothing constant
stable
tracking signal
trend
9. inventory fundamentals
there are benefits as well as costs to having inventory. the problem is to balance the cost of carrying inventory with the following;
- customer service : the lower the inventory level, the higher the likelihood of stock out and the potential cost of back order, lost sales, and lost customers. the higher the inventory level, the higher the level of customer service
- operation efficienfy: inventory decouple one operation from another and allow manufacturing to operate more efficiently. they allow leveling production and avoid the costs of changing production level. carrying inventory allows longer production runs and reduces the numver of setups. finally inventories let manufacturing purchase in larger quantities. the ABC inventory classification system prioritize individual item so that inventory and costs can be better controlled.
- cost of placing orders : inventory can be reduced by ordering less each time an order is placed. however, this increases the annual cost of ordering.
- transportation and handling costs: the more often goods have to be moved and the smaller the quantities moved, the greater the transportation and material handling costs.
- inventory management is influenced by several factors
- the classification of the inventory, whether raw material, work-in- process, or finished goods.
- the function that inventory serves; anticipation, fluctuation, lot size, or transportation.
- supply and demand pattern
- the costs associated with carrying (or not carrying) inventory.
besides managing inventory at the aggregate level, it must also be managed at the item level. management needs to establish decision rules about inventory items so inventory control personnel can do their job effectively.
key terms
a items
ABC inventory
anticipation inventories
asset
average cost
balance sheet
c item
capacity-associatd costs
capital
carrying costs
cost of goods sold
cycle stock
days of supply
decouping inventory
distribution inventory
expenses
finished goods
first in first out
fluctuation inventory
general and administrative espenses
hedge inventory
income
inventory profiling
inventory turns
inventory velocity
item cost
landed cost
last in first out
liabilities
lot-size inventories
maintenace, repair and operating
supplies(MROs)
owner's equity
pareto's law
pipeline or movement inventories
raw materials
retained earnings
return on investment
revenue
safety stock
standard cost
stockout
transportation inventories
work-in process( WIP)
10. order quantities
the economic order quantity is based on the assumption that demand is relatively uniform. this is appopriated for some inventories. and the EOQ formula can be used with reasonable resutls. one probelm in using the EOQ formula is in determining the cost of odering and the cost of carrying inventory. since the total cost curve is flat at the bottom, good guesses vary often will produce an order quantity that is economical. it has also been demonstrated that the EOQ concept can be used effectively with groups of item when the cost of carrying and ordering are not known.
the two costs influenced by the order quantity are the cost of ordering and the cost of carrying inventory. all methods of calculating order quantities attempt to minimize the sum of these two costs. the period order quantity does this. it has the advantage over the EOQ in that it is better for lumpy demand because it looks forward to see what is actually need.
key terms
economic order quantity
fixed order quantity
lot-for-lot
min-max system
noninstantaneous receipt model
period order quantity
quantity discounts
stockkeeping units(SKU)
11. independent demand ordering system
this chapter addressed the problem of when to order, whereas chapter 10 addressed the problem of how much to order. system for ordering should be simple to use, such as an order point system or a periodic review system. ordering systems need to ensure orders are placed in time to avoid running out of stock.statistical applications allow a prediction of the demand duting the critical lead time to establish safety stock. the order point uses this safety stock plus anticiated demand duting the lead time to ensure aceptable service to the customer. distribution system can take advantage of MRP type logit to optimize order quantities all the way through the supply chain. inventory and ordering systems are all affected by the lead time.; discussion of techniques of shortening the lead time si subject of most of the chapters in this book.
key terms
average or mean
centralized system
decentralized system
dispersion
distribution requirements planning
kanban systme
lead time
normal curve or bell curve
normal distribution
order point
permanent or static information
perpetual inventory record
safety factor
safety lead time
safety stock
standard deviation
target-level or maximum-level inventory
two-bin systme
variable or dynamic information.
12. pysical inventory and warehouse management
previous chapters in this book have used thoery and common sense to effectively manage inventories. this chapter looks at the physical handling and storage of inventory. warehousing is chaging from a place to simply store material to a strategic actibity affecting a major investment to companies and a significant factor in improving customer serviece. the basic warehouse activities of receiving, identifying , storing, retrieving, and evnetually shipping goods are all still required, but technology and the need for speed in the supply chain are changing the way we do things. ' a place for everything and everything in its place' has given way to floating location and point of use storage. as movements are being sped upm there is an increasing ned for controla and security, and it is important that workers know and understand proper procedures and the consequences of error. to provide high levels of customer service, inventory records must be accurate. cycle counting improves record accuracy but, more importantly, find erroe in the inventory systems so that processes can be continually improved. bar code and RFID technologies are widely used in any modern inventory and warehousing system, improving data accuracy and speeding the movemnet of product. consigment inventory and VMI are changing the replenishment of inventory and impact issues of inventory storage.
13. physical distribution
Physical distribution is the movement of goods into and out of a company and is changing in both the global company and in the individual delivery of goods to internet customers. the majority of goodds are still shipped in large economical units through distribution channels. third and fourth party logistics provides are applying their area of specialization to help companies drive down costs while improving customer service. sound packaging design is critical to a company not only because it affects the efficient handling of product all the way through the supply chain but also because it can have a high enviormental cost. reverse logistics along with a change in the distribution channel to internet customer is another reason for the growth of 3pls. warehouses strategically placed through the supply chain can help provide improved customer service and reduce costs.
the global sourding and distribution of goods across international boundaries has increased the need for accurate, comprehensive documentation to determined things such as who pays the freight, who prepare the documentation, who own the goods, and who may be responsible for any environmental problems. incoterms, standard terms accepted around the world, address most of these concerns and are a requirement of any freight movement. scheduling of shipments is a critical part of physical distribution in order to optimize transportation methods while taking speed, cost, and customer's need into consideration.
14. products and processes
products and the processes used to make them are continually being redesigned to create products more appealing to customers, to improve productivity, or to make the products and their associated processed friendlier to the enviorment. producers follow well established principle of product development the 3Ss, simplification, standardzation, and specialization, are very powerful principles that can help to improve productivity and make products more reliable. with information easy to share in today's environment, product design and process design can wrok simultaneously to bring better quality products to market faster and with reduced costs. as the design of the product is being established, the proces is also being designed based on the quality level desired, the ability of the process to react quickly to changes in customer demandI(flexibility), the overall volume of demand, and how much the customer wants to be involved in the production of the product. depending on the volume, the decision may be made to buy the product rather then make it, or to use one process rather than another. this is best determined with the cost equalization poin(CEP),which determineds a volume below which the low fixed costm high variable cost alternative is used, and abobe thich a company may invest in the high fixed cost and low variable cost alternative.
continuous process improvement(CPI) applies to all processes to make them more cost effective and competiticve, it's done on an ongoing basis, not just when new products are introduced. CPI uses the traditional tools of the scientific methods in six steps; select, record, analyze, develop, implement, and maintain. all the steps have one thing in common and that is the involvement of people.
with improvements to product and process, design goods tend to flow quickly and smoothly, resulting in lower costs and improved profits. continuous improvement leads to the next chapter in thei test on just in tiem and lean production.
15. lean production
the lean production philosophy and techniques that seek the elimination of waste and continuous improvement were developed for repetitive manufacturing and are perhaps most applicable there. however, many basic concepts are appropriate to any form or manufacturing organization. they are noe also being adapted and adopted by service-oriented operation as well.
waste can be caused by poor product design or the manufacturing process it self.seven types of wast include processing, motion, trasportation, defectm waiting time, overproduction, and inventory. poka-yoke techniques can be applied to elminate the ability to produce defects.
major concepts with lean production include flow manufactuing, process flexibility, quality management, total productive maintenace, uninterrupted flow, continuoust process improvement, supplier partnership, and total employee involvement. puch systems are replaced by pull systems, and the work authorized by the use of kanbans or signals, for replenishment of inventory.
other tools utilized within lean production include value stream mapping, kaizem, takt time, 5S housekeeping, and visual management. accounting must also change in a lean enviorment, and be focused on measuring the costs and savings associated with the elmination of waste and continous improvement.
the lean production enviroment requires a planning and control system. the enter-prise resource planning systme is complemenraty to lean production and JIT. the way in which some functions are used changes to reflect the difference in the manufacturing enviroment, but in general, the tools are advantageous by utilizing the elements in each that work best in that enviroment.
16. total quality management
quality of both products and services is ultimately established by the customer and the custmer is continuously setting higher and higher standards. a company's commitment to qualtiy must start with top management to ensure the entire company works toward improvements. a commitment to qualtiry determines everyghin from the design policies of products and services, to the design of the production processes, to the qualtity of supplyers and finally to the end use by the consumer. worker involvement is essential since they have direc knowledge of the processes used and are the first to be aware of any changes.
the technical aspects of quality focus on reducing variation and the factors that cause variation of both common cause and assignable cause. statistical tools are readily available to study variation and calculators and computers take a lot of the drudgery out of the calculation. whre possible, it is important to control the process rather than the procues itself. sampling plans test products after they are produced and do not directly impove the qualtiry of products. but sampling is still necessary when the cost of failure are high in industries such as pharmaceutical and aerospace.
management can follow many accepted programs such as ISO standard, six sigma, or QFD to drive qualtity improvements. high quality is a necessary part of lean production as companies work with lower inventoris and faster product flow
'스터디스터디 > CPIM' 카테고리의 다른 글
[schedule]CPIM Part 1 - 230328 (0) | 2023.03.20 |
---|---|
[Completed]핵심문제 (0) | 2023.03.20 |
[completed] 11과 Indepenced Demand Ordering Systems (0) | 2023.03.16 |
[completed] 16과 Total Quality Management (0) | 2023.03.16 |
[completed] 10과 Order Quantities (0) | 2023.03.16 |